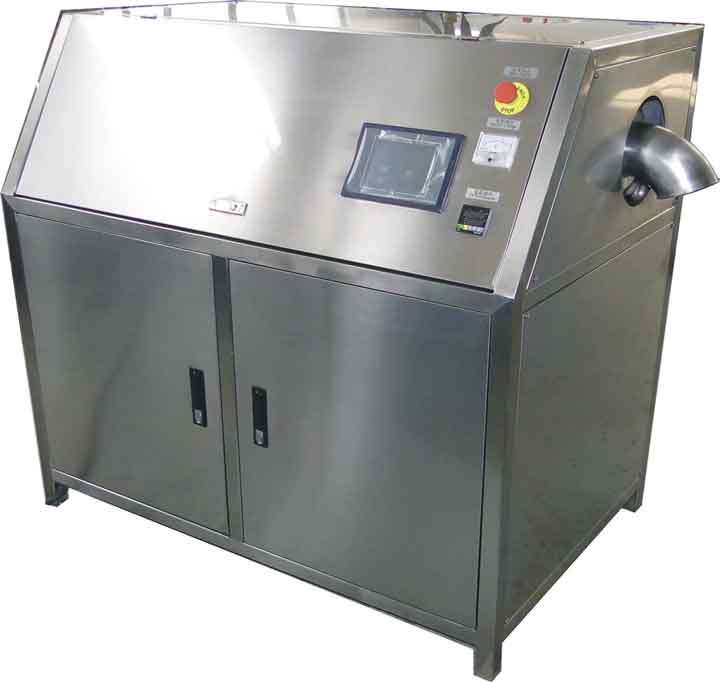
Contents
1. General introduction
2. Hydraulic system
3. Electric control system
4. Installation and commission
5. Operation
6. Maintenance
7.Trouble shooting
General introduction
Dry ice pelletizer is a dry ice machine which makes dry ice pellets of liquid Co2.
- Overall dimension is L1450*W800*H1250mm, the net weight is 580kg
- Production capacity
Dry ice size: Dia.3mm and 16 mm;
Dry ice density: food grade ≥1.50
Dry ice capacity:50kg per hour
- Co2 and Ice conversion rate≥40%
- water content of liquid Co2 <50ppm;liquid Co2 input pressure≤2.0MPa。
Warning: It is forbidden to start ice machine if there is change on filling or pressure of liquid Co2 store tank.
5、Co2 gas comes out through one pipe with flange easy for recovery if necessary; and air discharge must keep open.
6、Total power is 3.7kw。
Hydraulic system
1、Technical specification
A. Max system pressure is 21MPa;
2、Normal working pressure is less than 18MPa;
3、pump flow is 31L/min;
4、motor power: 3.7KW;
5、oil tank 140Litre;
6、oil tank size is 80*45*40mm
2、National standard 46#, 56#,68# new anti-wear hydraulic oil (Hydraulic oil should be 17-23 CST on kinematic viscosity and oil pollution should be below grade 12, NAS standard.); fill oil through oil hole to top-limit of oil gauge(around total 350L hydraulic oil required). Clean each 6months and replace oil each 12months.
3、System pressure test
Motor is connected wire according to Δwire connection method and ensure the right clockwise direction. Start oil pump, adjust overflow valve to control system pressure. The value of system pressure will be shown on left side pressure gauge. And this system pressure is 21 MPa. Suggestion: it is better to select the smaller pressure if it meets power requirements of machine. In this way, power consumption can be lowered; we have adjust this system pressure well between 18-21 Mpa before machine leaving factory.
4、Pressure relay test
Pressure relay has been tested and adjusted well before machine leaving factory. At normal work, if it starts too early or no any motion, pressure relay can be adjusted by the button at the end of pressure relay manually; to increase pressure by clockwise and to decrease pressure by anticlockwise way.
5、Notice:
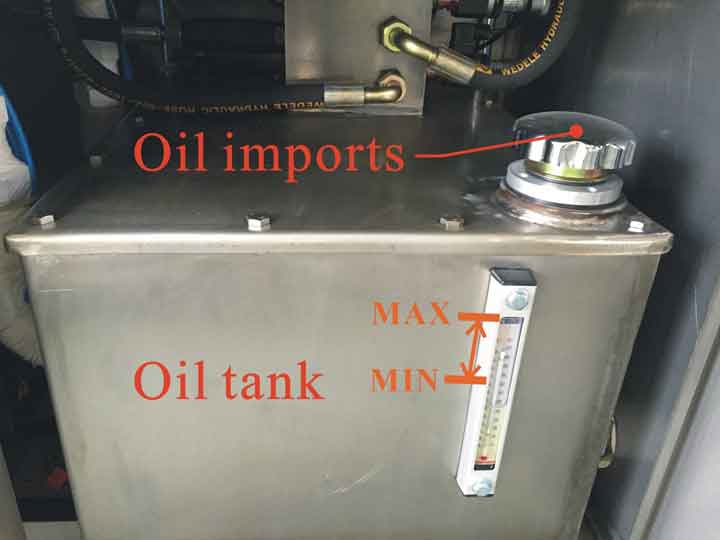
A, oil level on the low side, suction oil filter will easily suction air and system will vibrate and the solution is: fill oil to oil tank and allow oil level over liquid indicator and idling oil tank several time to expel air out of tank.
B, Clean suction oil filter every 6 months.
C, the voltage of solenoid directional valve and solenoid overflow valve is 220V, so to ensure voltage not lower than 220V.
Electric controls system
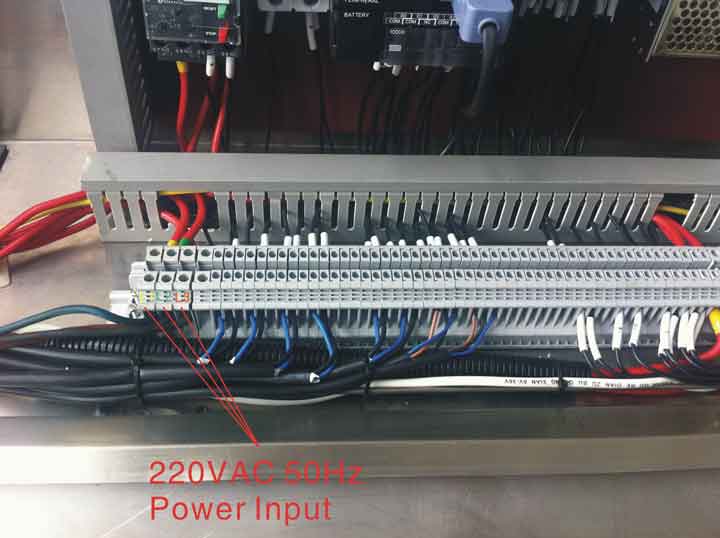
Inlet wire is three phase four wire and size is 2.52mm; Connect power inlet wire and zero line of 220VAC, 3phase 50Hz into inlet wire box on top right of machine and screw it according to electric regulations.
Warning: the machine must be safely grounded!
Installation and commission
1Installation
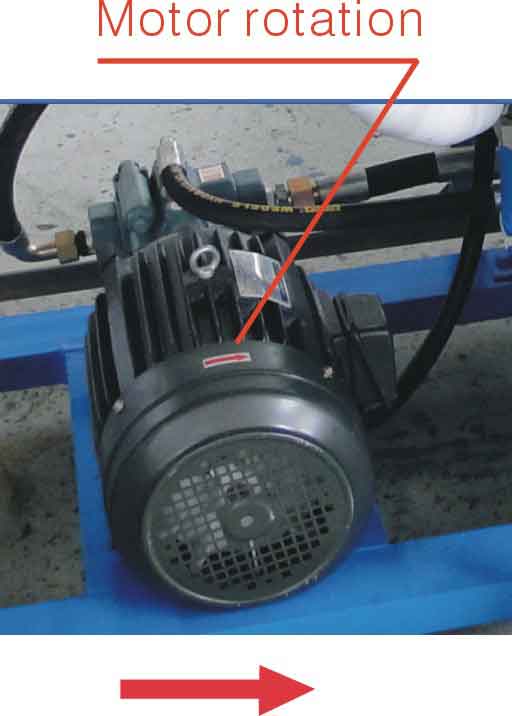
The ground must be flat and smooth and please fasten the feet of machine. Delivery pipe and valve diameter should be not less than φ10, pressure is 1.6~2.0MPa and liquid pipe must be insulated.
Warning: dry ice making shop should be well ventilated!
2 start ice machine
(1)open electric box, push on shunt circuit breaker;
(2)switch on main power in inlet wire box;
(3)loose the “stop” button on board;
(4)start oil pump motor on touch screen;
(5)operate on touch screen for all steps.
Note: A.please observe if the motor runs clockwise during first time start.
B.after starting oil pump, you can manually adjust hydraulic system pressure and switch action pressure; system pressure is 21MPa when machine leaving factory.
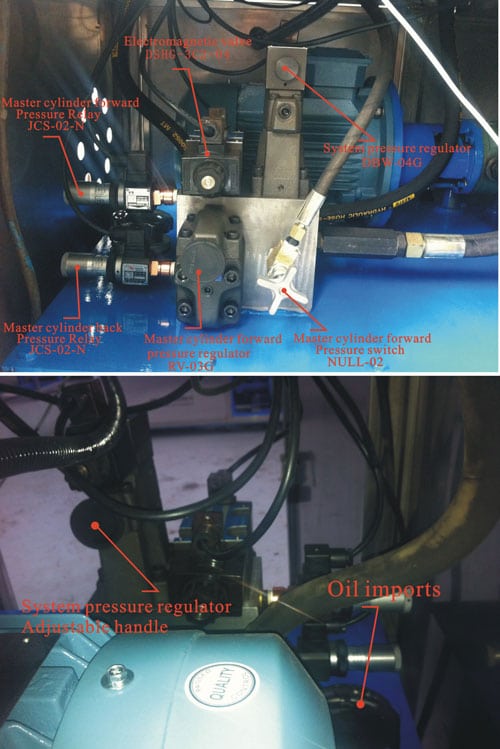
Warning: It is strictly prohibited to reverse the oil pump
(6)set feeding time and pressure retaining time according to processing requirement;
(7)choose manual or automatic running mode;
(8)shut off all power after work.
Operation
1 first open manually valve of liquid pipe outside and let liquid Co2 come into machine.
2、then start power, oil pump, mixing motor; press main cylinder advancing and back, feeding 10 seconds, then press main cylinder advancing and back, feeding 10 seconds, and repeat such action several times.
Note: Feeding action is only started when main oil cylinder is at rear end;
Automation action is only started when main oil cylinder is back to end.
3、Dry ice will be made automatically when compression box is cooled completely.
Notice: each time start machine, there is a lot of Co2 gas existing in pipes, users must blow compression box and dew by the Co2 gas.
4、Dry ice adjusting
A, adjust output of dry ice by adjusting add Co2 time parameter: the adjusting parameter for YGBK-50-1 is 0.4-0.5KG. If it is less 0.45kg, it will effect ice output and if it is more then 0.5kg, it will effect Co2 gas discharge and bad for machine.
B, adjust size of dry ice
The length of dry ice can be adjusted by the adjusting speed of mixing motor.
Different mould can produce different size of dry ice pellets fromΦ3-Φ16.
Warning:
A Piston must be pushed at bottom when feed manually.
B when feeding solenoid valve cannot shut off, shut off feed ball valve (offered by user )immediately. C ice output at one time cannot exceed 0.5kg.
C it is forbidden to put your hands near the closing door of the compression box when the oil pump is running.
D Co2 is not toxic but high-density Co2 can make people suffocate; so it is necessary to keep dry ice factory well ventilated.
E solid form of Co2-dry ice, minus 78℃, can easily frostbite skins, so suitable insulation measures are a must when touch dry ice.
D dry ice easily sublimates and its expansion rate is 600 when it changes to gas; so it is not right to store dry ice in a completely sealed place with no gas out way.
Maintenance
1Should clean liquid Co2 in all pipes when machine stops working; after electricity disconnected, should clean the machine body and dry it by cloth.
2Check if there is oil leaking; if there is oil leaking, tighten the screws or replace sealing ring.
3Check if there is paint off; if there is paint off, brush paint in case of rust.